



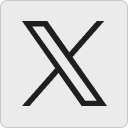

This story begins back in August at the KIM Conference, when Dorel Senior Product Marketing Manager, Ryan Hawker, pulled Kecia and me aside and told us excitedly he had something to show us. That something was the Scenera NEXT and the official launch for this awesome little seat was on Saturday at the Dorel Technical Center in Columbus, IN, where they manufacture the NEXT and other Dorel carseats. Honored for the invitation to the launch, I had to battle Darren, Kecia, and Jennie for who would go to the event. Unfortunately for Darren and Kecia, they had already visited the Dorel Technical Center several years ago when it first opened; Jennie’s daughter, it turns out, had a recital that day. Win for Heather!
The Dorel manufacturing facility is indeed enormous at 1.1 million square feet. They do everything here from designing carseats to 3D printing for testing to manufacturing to storage and shipping. We started our tour of the facility at the Technical Center. Everyone had done a great job of setting it up for fun! There were balloons anchored by locking clips everywhere. All employees were wearing Scenera NEXT t-shirts. The launch event wasn’t just a tour for the blog and two other invited dignitaries (That makes us sound important, doesn’t it? Ha!). No, it was for the families of those who work on the NEXT to come in and see what their family members do at work. This was the first time Dorel had done an event like this and also the FIRST time they’d gotten a carseat from idea to production in a YEAR. That’s unheard of in carseatland.
We started in the foyer of the Technical Center where they had a few NEXT fashions shown, then we moved into a room with a big screen where they were showing a video of kids explaining the features of the NEXT. All 13 fashions of the NEXT were there—unfortunately it was very dark and there was no way I could get a good picture. Trust me, you’ll love them all. They had face painting for the kids off to the right in the open offices—you can tell this is a carseat company since there are carseats laying about everywhere. They weren’t just new carseats either. Ancient carseats in pristine condition lined one wall—oh wait, they’re still a few years younger than me.
We next visited the 3D printing room where 2 printers work to make test pieces. When an engineer designs a part and wants to know if it will work a certain way, he or she sends a CAD file here and it’ll get printed up. Sometimes the part is sturdy enough to be installed on the test seat located in the room.
Just a few feet down the hall is the crash testing lab. They were running crash tests about every 5 minutes so everyone could get a chance to see one. The crash tests happen so fast you have to be standing and looking at just the right spot to see it happen. Even then, if you blink, you miss it. That’s truly how fast it happens. Fortunately, they had a slo-mo video at the other end of a different test that we all shuffled down to watch. Because they weren’t setting up a new seat after each test, I asked Ryan if they had ever done multiple crash tests on a seat before. He said they hadn’t and were using this as an opportunity to see how this carseat held up. I didn’t look carefully at the seat they were using, but I believe it was Safety 1st Complete Air.
On our way to see the NEXT actually being molded, we came across 2 carseat mold forms—about 4′ tall—sitting on the floor. Ryan explained that the mold comes in 2 halves, which are pressed together under great pressure. The plastic is injected into the mold, cooled, then removed from the mold by robots for more cooling, removing of sharp plastic bits, and label application. Next the seat shells are transported by conveyor belt to human hands for wicked fast assembly of the rubber plugs that help the NEXT grip the vehicle seat, harness adjuster strap, tether assembly, harness, LATCH strap, and cover. The final step in the process is a computerized camera and laser quality assurance check that makes sure *everything* on the carseat has been assembled perfectly. If it hasn’t, an alarm is sounded and it gets pulled and checked for errors. Each carseat is stored in a database so it can be tracked if a customer calls about it.
We ended our tour where most employees begin their day: at the Shining Star wall. When they clock in, employees pass a wall filled with stories where Dorel carseats have saved lives. Handwritten thank you letters with pictures of carseats and crashed vehicles are posted on the wall and a notebook is kept to the side to keep older letters as new ones arrive. It goes to show that when you share your story with the people who create the carseat your baby rides in, whether your baby is a few hours old or several years old, they know about it and appreciate it.
After going through the facility and meeting the people behind Dorel and Cosco, I came away with a powerful feeling of family and pride. We ran into many 2nd generation employees as we made our way through and they were so proud to share their jobs with us and their families, who had never been to the factory floor before. All the families were dressed up and it was clearly an important and fun day for everyone and all for the launch of a new little carseat destined to take the carseat world by storm.
We have a mini-review of the Cosco Scenera NEXT in our Comparison of Budget Priced Convertibles under $100 and will have a full review soon. Stay tuned for a giveaway! The NEXT is available for purchase for $49 from Walmart.com.
Of course, my trip to Indiana would not have been possible if not for the invitation from our Cosco friends and 360 Public Relations. Thank you for sharing the day with me and allowing me to see your processes and the pride behind the products.
Very cool. I’m impressed, too. (-; Thank you for sharing your tour!!
Ok, the laser quality check kind of just blew my mind. That’s super cool. THE FUTURE IS NOW
How exciting! Very cool, Dorel 🙂